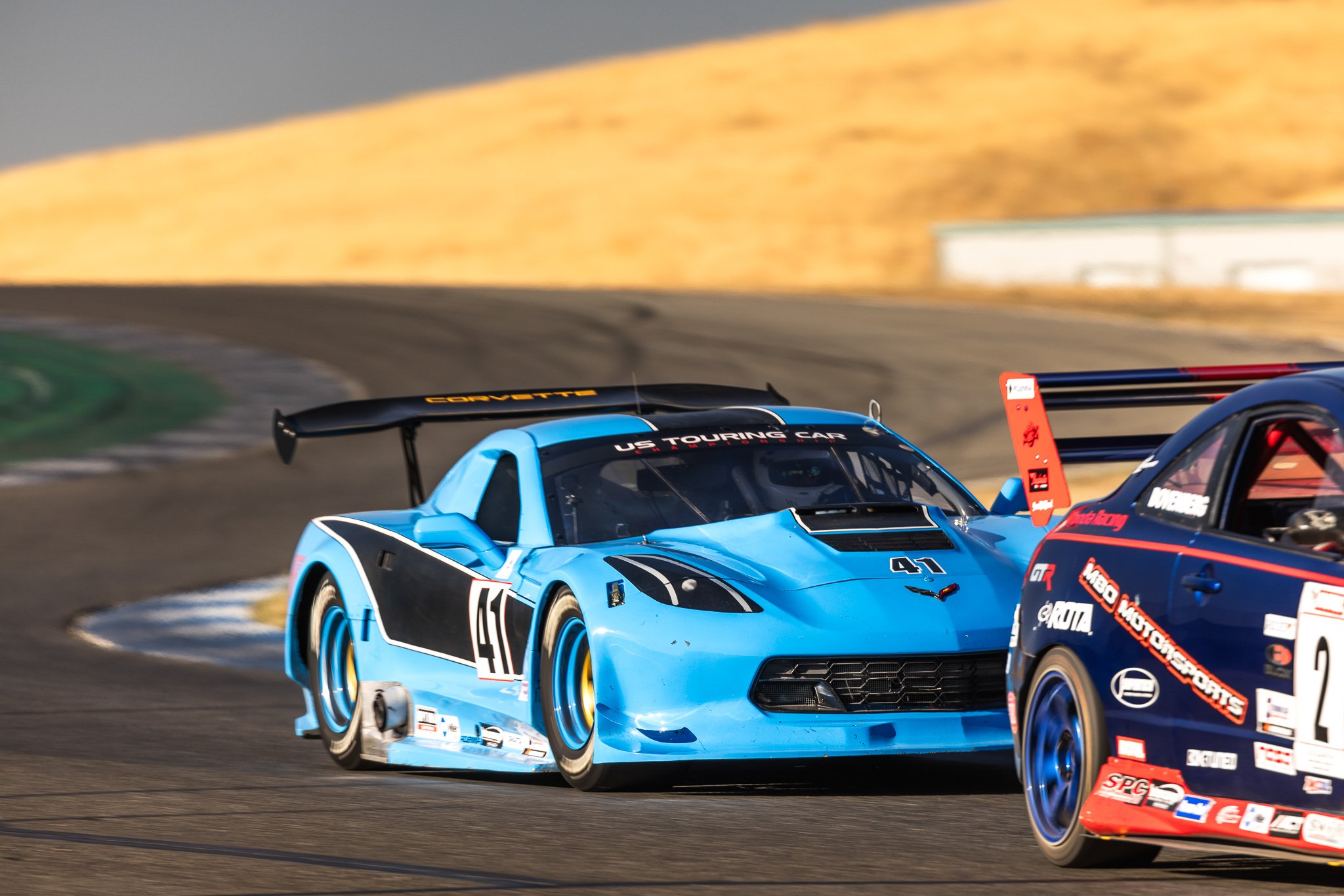
SpeedSF Blog
Every Build Has a Story – Meet the Cars of SpeedSF

CSG Brake Pads: Details Make the Difference
Thanks to a detailed feedback loop between CounterSpace Garage and their wide array of active customers, they've been able to provide a usable, confidence-inspiring brake pad for every popular HPDE platform today.